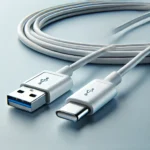
The Key Advantages and Features of USB Data Cables
2024-11-11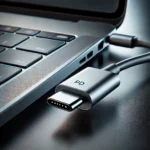
Unlock the Power of PD Protocol with the Ultimate Type-C Interface Combination!
2024-11-12Introduction to Electrical Insulation
Electrical insulation is a crucial part of electronic wiring systems. Its main purpose is to prevent unintended electric current flow, protecting both devices and users. Insulation acts as a barrier, separating the conductive parts of wires and preventing contact with external conductive surfaces. Without proper insulation, the risk of short circuits, shocks, and fire hazards increases.
The materials used for electrical insulation vary widely, each with unique properties suited to specific applications. Common materials include plastics such as polyvinyl chloride (PVC) and polyethylene, rubber, and fiberglass. These materials possess excellent dielectric properties, meaning they can withstand electric fields without conducting current. This ability is critical for maintaining electrical safety in numerous devices, from household appliances to industrial machinery.
Good insulation is not just a protective measure. It helps electrical systems run efficiently, minimizing energy loss and reducing overheating risks. In environments with moisture, heat, or chemicals, high-quality insulation is essential. Poor insulation can endanger both devices and users.
In conclusion, selecting the right insulation materials is key to ensuring electrical safety. As technology evolves, investing in high-quality wires and insulation becomes more critical. This underscores the need for strict safety standards in the industry.
The Importance of Qualified Insulation
Qualified insulation is essential for electrical safety. It ensures that electronic wires function properly and electrical systems stay intact. Insulation prevents electrical shorts and protects users from electric shocks. When insulation doesn’t meet qualifications, it can lead to dangerous failures and fires.
One key reason for choosing certified insulation is to prevent thermal overload. Unqualified insulation may not withstand heat, causing it to degrade. This can lead to short circuits and system damage. Insulation that isn’t certified might also lack the necessary dielectric strength, increasing the risk of electrical breakdowns. This can disrupt devices or pose safety risks to users.
In addition to failures and hazards, improper insulation can violate safety regulations. Regulatory bodies enforce standards to protect consumers. Businesses that use unqualified insulation may face legal and financial consequences. By choosing certified materials, companies show their commitment to safety, reducing the risk of accidents and lawsuits.
In conclusion, qualified insulation is vital for preventing risks like electrical failures and fire hazards. It ensures the reliability and safety of electrical systems.
Common Types of Insulation Materials
Insulation materials play a critical role in the functionality and safety of electronic wires. The choice of insulation can influence not only the performance of the wires but also their safety in various applications. Among the most commonly used insulation materials are Polyvinyl Chloride (PVC), rubber, and Teflon, each offering unique properties and advantages.
PVC is widely favored for its versatility and cost-effectiveness. It provides a decent level of electrical safety and is resistant to abrasion, making it suitable for a range of household and industrial applications. However, unqualified PVC insulation may pose risks, such as a reduced capacity to withstand high temperatures, leading to potential overheating and even failure of the electrical systems it protects.
Rubber insulation is another popular choice, known for its excellent flexibility and resilience. This material is particularly advantageous in environments subject to extreme bending or movement. Rubber can effectively handle fluctuations in temperature and is resistant to moisture, making it ideal for outdoor use. Nonetheless, if the rubber insulation is unqualified or of low quality, it may degrade faster than expected under harsh conditions, exposing the underlying wires and increasing the risk of electrical accidents.
Teflon insulation is recognized for its high-performance characteristics, offering superior heat resistance and low friction. This material is particularly beneficial in high-temperature environments and is commonly used in aerospace and automotive applications. Although Teflon’s advantages are substantial, unqualified Teflon insulation can lead to brittleness over time, which could result in cracks and compromised electrical safety in wiring systems.
Understanding these common insulation materials and their properties is essential for ensuring the safety and reliability of electronic wires. Unqualified insulation can lead to a variety of hazards, emphasizing the importance of adhering to industry standards when selecting insulation materials.
Real-World Consequences of Poor Insulation
Poor insulation in electronic wires can lead to devastating consequences in both residential and industrial settings. Insufficient insulation, whether due to substandard materials or improper installation, can create significant risks, including electrical fires and equipment failures. A notable example occurred in 2019 when a commercial building in Philadelphia suffered a catastrophic fire linked to improperly insulated wiring. The blaze resulted in extensive damage, estimated at $2 million, and the displacement of numerous tenants. Investigations revealed that the insulation used was not adequate for the electrical load, highlighting a failure to adhere to electrical safety standards. Such incidents underscore the pressing need for quality when selecting electronic wires.
Statistics paint a concerning picture. According to the National Fire Protection Association (NFPA), electrical fires caused by faulty wiring account for an estimated 51,000 incidents annually in the United States alone. An alarming percentage of these cases is attributable to substandard insulation. These fires are not only perilous, resulting in injuries and fatalities but also create substantial financial strain on businesses and homeowners alike. The cost associated with these fires extends beyond immediate damage, encompassing legal fees, loss of property value, and increased insurance premiums.
Moreover, equipment failures resulting from inadequate insulation can disrupt operations and lead to significant downtime for businesses. A report from the International Electrotechnical Commission suggests that electrical equipment failures can cost companies as much as $1 million per incident in lost productivity and repairs. As a result, the implications of poor insulation resonate far beyond individual incidents, affecting supply chains and consumer trust, significantly impacting economic stability. Ensuring the integrity and quality of electronic wires is crucial for preventing these adverse consequences and safeguarding the well-being of both consumers and businesses alike.
Identifying Unqualified Insulation
When dealing with electronic wires, it is crucial to ensure that the insulation meets safety standards. Unqualified insulation can pose significant risks, leading to electrical failures or hazards. Identifying inadequate insulation begins with a careful examination of the wiring. One of the first things to consider is the visual condition of the insulation itself. Look for any signs of wear and tear, such as cracks, fraying, or discoloration. These visual cues can indicate that the wiring may not be suitable for use and could compromise electrical safety.
Additionally, it is essential to check the labels on electronic wires. Reputable manufacturers provide clear specifications regarding the type of insulation used and its safety ratings. When purchasing wires, ensure that they comply with established safety standards, which usually include certifications from recognized organizations. Labels should also indicate the temperature rating, which is crucial for ensuring that the wire can handle the electrical load safely without overheating.
Furthermore, familiarize yourself with the different materials used in insulation. Common types include PVC, rubber, and Teflon, each offering varying degrees of protection against environmental factors such as moisture, heat, and chemicals. Understanding the characteristics and limitations of these materials can assist you in making informed decisions when selecting wires.
When inspecting existing installations, pay attention to the overall installation practices as well. Improper techniques, such as excessive bending or pulling of wires, can compromise the integrity of the insulation. Taking these steps to identify unqualified insulation in electronic wires is key to maintaining electrical safety. Proper identification and timely intervention can prevent hazardous situations and contribute to a secure electrical environment.
Industry Standards and Regulations
Insulation in electronic wires is critical for maintaining electrical safety and ensuring the reliable operation of electrical systems. Various industry standards and regulations play a fundamental role in governing the quality and effectiveness of this insulation. Prominent organizations such as the American Society for Testing and Materials (ASTM) and the International Electrotechnical Commission (IEC) are at the forefront of developing these standards. They provide guidelines and criteria for the testing and evaluation of insulation materials used in electronic wires, thereby contributing to the overall safety of electrical systems.
ASTM develops comprehensive standards that cover a wide range of materials, including those that are used for insulating electrical wires. These standards address critical properties such as thermal stability, dielectric strength, and resistance to environmental factors. By adhering to these established guidelines, manufacturers can ensure that their products meet or exceed the necessary safety requirements. This adherence not only enhances the quality of the insulation but also reduces the risk of electrical failures or hazards that could lead to severe consequences.
Similarly, the IEC provides international standards that facilitate the safe design and installation of electrical components and systems. The integration of their standards helps manufacturers and consumers alike to maintain compliance across different countries, increasing the overall safety of electrical products globally. For consumers, understanding these standards is paramount as it enables them to make informed choices regarding the electrical wires they select for their projects. By choosing products that are compliant with ASTM or IEC standards, buyers can considerably improve their electrical safety.
In conclusion, awareness of the industry standards and regulations governing insulation in electronic wires is essential for both manufacturers and consumers. By ensuring compliance with these standards, not only is electrical safety enhanced, but the risks associated with unqualified insulation can be mitigated significantly.
Preventive Measures Against Insulation Issues
To mitigate risks associated with unqualified insulation in electronic wires, it is imperative to adopt preventive measures that ensure both safety and longevity of electrical systems. One of the foremost recommendations is to implement proper installation practices. This involves using high-quality electronic wires that adhere to established electrical safety standards and regulations. Hiring a licensed electrician with proven expertise in the installation of electrical systems can significantly reduce the likelihood of insulation failures. A qualified professional is equipped to identify potential hazards and ensure that all components are correctly fitted and rated for their intended use.
Regular maintenance checks are another critical aspect of maintaining the integrity of insulation in electronic wires. Conducting routine inspections can help detect early signs of wear, damage, or degradation caused by environmental factors such as moisture or extreme temperatures. Particularly in industrial or commercial settings where the demand for electrical safety is paramount, scheduled maintenance can prevent costly failures and promote operational efficiency. During these inspections, it is essential to examine not only the insulation but also the connections and surrounding elements that could impair the performance of the electronic wires.
Furthermore, it is advisable to stay informed about best practices in electrical safety, including updates in technology and material standards. Investing in ongoing training for staff members who handle electrical equipment ensures that they remain vigilant and knowledgeable about potential hazards related to insulation. Lastly, if any concerns arise regarding insulation quality or insulation compatibility with existing systems, individuals and businesses should not hesitate to consult qualified professionals. A proactive approach, supported by expertise, can significantly reduce the risks associated with subpar insulation and bolster overall safety in electrical applications.
Future Trends in Insulation Technology
As technology continues to evolve, so does the demand for advanced insulation materials in electronic wires. Research in this field is increasingly focused on developing solutions that not only enhance electrical safety but also contribute to overall efficiency and sustainability. One prominent trend is the shift towards the use of high-performance polymers. These materials offer superior thermal resistance and dielectric properties, making them ideal for insulating electronic wires in applications that demand high reliability in strenuous environments.
In addition to polymers, bio-based materials are gaining attention for their eco-friendly attributes. Researchers are exploring the feasibility of natural fibers and biodegradable substances, which align with the growing movement towards sustainability in the manufacturing sector. Such innovations not only help reduce carbon footprints but also improve the overall durability of electrical insulation, ensuring long-lasting performance without compromising safety.
Another exciting development is the incorporation of smart technologies into wire insulation. This can include sensors embedded within the insulation layers that monitor temperature, humidity, and electrical flow in real time. These advanced electronic wires equipped with smart insulation could significantly enhance electrical safety by providing instant alerts in cases of overheating or potential failures, enabling timely intervention and preventing accidents.
Moreover, the industry is witnessing advancements in multi-layer insulation designs. These include various material combinations that enhance conductivity while maximizing safety. Multi-layer constructions can also facilitate the reduction of electromagnetic interference, which is critical in modern electronic applications. As the demand for high-speed and efficient electrical systems grows, such innovations are essential in meeting the future needs of the market.
These trends signify a promising future for insulation technology in electronic wires, prioritizing safety, efficiency, and sustainability in electrical applications.
Conclusion: Prioritizing Quality in Insulation Choices
In today’s technologically driven world, the integrity of electronic wires is paramount for ensuring electrical safety. Throughout this blog post, we have highlighted critical aspects of insulation material selection and the potential risks posed by opting for unqualified options. Such choices not only jeopardize the longevity of electronic systems but also create a significant hazard to both users and equipment.
The quality of the insulation surrounding electronic wires plays a crucial role in maintaining electrical safety. Adequate insulation helps in preventing unwanted current leakage, which is essential for protecting circuits from overloads and short circuits. Furthermore, subpar insulation can lead to serious consequences, including electrical fires, equipment damage, and personal injuries. Stakeholders involved in the manufacturing, installation, and maintenance of electronic systems must remain cognizant of these risks, emphasizing thorough evaluations of insulation materials involved in their wiring systems.
Moreover, regulatory standards exist to guide the choice of insulation to ensure optimal performance and safety. Familiarizing oneself with these standards is vital for anyone involved in the selection of electronic wires and their insulation. It is imperative to engage qualified professionals who understand the nuances of insulation materials and their applications. This proactive approach can significantly mitigate risks associated with electrical safety, ensuring that insulation choices contribute positively to overall system performance.
Ultimately, remaining vigilant about the quality of insulation in electronic wires cannot be overstated. By prioritizing well-qualified materials, we safeguard not only the functionality of our electrical systems but also protect the well-being of individuals who interact with them. As technology continues to evolve, sustaining an unwavering commitment to proper insulation standards will be fundamental in overcoming the hidden dangers associated with inadequate electronic wire insulation.
Learn about the safety certifications and standards for insulation materials used in electronic wiring to ensure compliance with industry regulations.
Outbound Link: UL Official Website
Access authoritative information on international electrical and insulation standards, ensuring global electrical safety compliance.
Outbound Link: IEC Official Website